주요 연구 성과
- Ph.D. Student Gisoo Lee and Professor Hansohl Cho, Extreme mechanics of heterogeneous soft crystals
- 관리자 |
- 2024-01-16 13:56:07|
- 988
Multi-component materials architected on crystal lattices have attained unusual, untapped multi-physical functionalities for a wide variety of engineering applications. The geometric and topological features in the constituents significantly influence the macroscopic functionalities in the multi-component heterogeneous materials in conjunction with the intrinsic material properties. Of recent interest are new opportunities to harness both mechanical resilience and energy dissipation capabilities in heterogeneous soft materials on crystal lattices. Furthermore, achieving outstanding performance in both mechanical resilience and energy dissipation has been a longstanding challenge in the design and manufacture of robust microstructural materials subjected to multiple, extreme cyclic loading scenarios.
In recent work led by Ph.D. student Gisoo Lee and Professor Hansohl Cho in the Department of Aerospace Engineering, KAIST, how connectivity characteristics can be employed to engineer elastic stiffness, flow stresses, shape recovery and energy dissipation as well as structural stability and reusability in heterogeneous soft crystals architected on Bravais crystal lattices (hard phase: gray, plastomeric material, soft phase: transparent, elastomeric material; see Figure 1) was demonstrated. In this work, they designed and constructed “dispersed” materials (staggered or stacked hard particles embedded in soft matrices) and their “interpenetrating” counterparts (through rod-connecting the first nearest lattice points by which both hard and soft domains are continuous) throughout different crystallographic lattices. Prototypes with dispersed-particle morphologies and its interpenetrating counterpart in the major crystallographic orientations were then fabricated using a high-precision multi-material 3D printer, and the large strain mechanical behavior of those materials were examined from quasi-static to high strain rate regimes. In both experiments and numerical simulations, the change in connectivity from dispersed-particle morphologies to interpenetrating morphologies resulted in significant increases in not only the elastic modulus but also in the flow stresses and energy dissipation during large strain loading and unloading conditions. The effect of adding connectivity on stress-strain behavior and energy dissipation was found to be strongly dependent on the crystallographic orientations and volume fractions of hard components. Furthermore, the increased energy dissipation within the interpenetrating morphologies negatively impacted the elastic shape recovery ability in all of these heterogeneous materials. However, the interpenetrating materials recovered their original shapes in a few minutes with no further physical treatment even beyond the end of unloading. The additional shape recovery was found to be mainly attributed to residual inelastic flow in the hard ligament network, in tandem with the residual elastic recovery capability in the soft domains. Interestingly, the interpenetrating materials recovered their original shapes much faster during high-speed impact loading conditions than quasi-static conditions due to the enhanced inelastic flow throughout the hard ligament network as the applied strain rate increases. Furthermore, the hard ligament network in the interpenetrating materials led to high reusability with no significant degradations in resilience, energy dissipation and load transfer capability under harsh, repeated loading and unloading cycles (up to a very large, imposed strain > 100%) from quasi-static to high strain rate regimes.
This work will guide further research in designing resilient yet energy-dissipative engineering materials and microstructures in diverse extreme environments. This work was supported by the National Research Foundation of Korea, and recently featured in Lee et al., Extreme resilience and dissipation in heterogeneous elasto-plastomeric crystals, Soft Matter, 20, 2023.
https://doi.org/10.1039/d3sm01076g
https://doi.org/10.1039/D4SM90006E
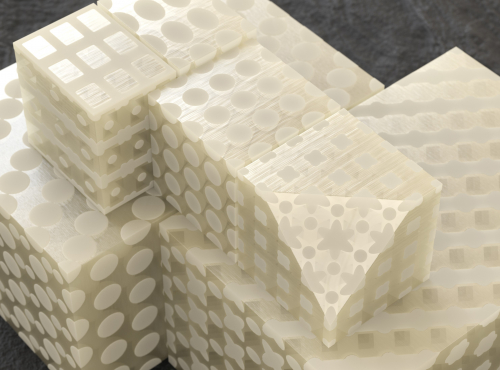
Figure 1: 3D-printed prototypes of heterogeneous soft crystals architected on Bravais crystal lattices.
In recent work led by Ph.D. student Gisoo Lee and Professor Hansohl Cho in the Department of Aerospace Engineering, KAIST, how connectivity characteristics can be employed to engineer elastic stiffness, flow stresses, shape recovery and energy dissipation as well as structural stability and reusability in heterogeneous soft crystals architected on Bravais crystal lattices (hard phase: gray, plastomeric material, soft phase: transparent, elastomeric material; see Figure 1) was demonstrated. In this work, they designed and constructed “dispersed” materials (staggered or stacked hard particles embedded in soft matrices) and their “interpenetrating” counterparts (through rod-connecting the first nearest lattice points by which both hard and soft domains are continuous) throughout different crystallographic lattices. Prototypes with dispersed-particle morphologies and its interpenetrating counterpart in the major crystallographic orientations were then fabricated using a high-precision multi-material 3D printer, and the large strain mechanical behavior of those materials were examined from quasi-static to high strain rate regimes. In both experiments and numerical simulations, the change in connectivity from dispersed-particle morphologies to interpenetrating morphologies resulted in significant increases in not only the elastic modulus but also in the flow stresses and energy dissipation during large strain loading and unloading conditions. The effect of adding connectivity on stress-strain behavior and energy dissipation was found to be strongly dependent on the crystallographic orientations and volume fractions of hard components. Furthermore, the increased energy dissipation within the interpenetrating morphologies negatively impacted the elastic shape recovery ability in all of these heterogeneous materials. However, the interpenetrating materials recovered their original shapes in a few minutes with no further physical treatment even beyond the end of unloading. The additional shape recovery was found to be mainly attributed to residual inelastic flow in the hard ligament network, in tandem with the residual elastic recovery capability in the soft domains. Interestingly, the interpenetrating materials recovered their original shapes much faster during high-speed impact loading conditions than quasi-static conditions due to the enhanced inelastic flow throughout the hard ligament network as the applied strain rate increases. Furthermore, the hard ligament network in the interpenetrating materials led to high reusability with no significant degradations in resilience, energy dissipation and load transfer capability under harsh, repeated loading and unloading cycles (up to a very large, imposed strain > 100%) from quasi-static to high strain rate regimes.
This work will guide further research in designing resilient yet energy-dissipative engineering materials and microstructures in diverse extreme environments. This work was supported by the National Research Foundation of Korea, and recently featured in Lee et al., Extreme resilience and dissipation in heterogeneous elasto-plastomeric crystals, Soft Matter, 20, 2023.
https://doi.org/10.1039/d3sm01076g
https://doi.org/10.1039/D4SM90006E
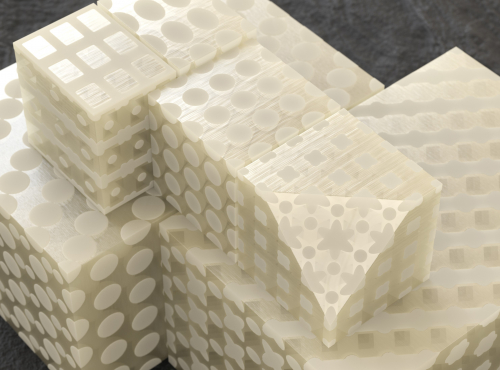
Figure 1: 3D-printed prototypes of heterogeneous soft crystals architected on Bravais crystal lattices.
첨부파일 |
---|
- 다음
- 한재흥 교수 연구실, 종이접기 기술 기반의 전개형 우주 방호 구조
- 2023-12-26